General
Capabilities |
|
Full
single-window integration between solid modeling and analysis |
|
Full
support of Windows® functions such as drag-and-drop,
point-and-click, and cut-and-paste |
|
Dynamic viewing (zoom, pan, rotate, sectioning) by mouse or
advanced 3D pointing devices |
|
Toolbars for fast access to main functionality |
|
Flexible model coloring and transparency control (parts,
assemblies, single or groups of faces, etc.) |
|
Direct use of CAD geometry for analysis |
|
Direct application of analysis input data to CAD geometry |
|
3D
visualization of analysis results on original CAD geometry |
|
FeatureManager™ for geometry, analysis and result
visualization data |
|
Customizable analysis tree |
|
Dynamic editing of all geometric and analysis features |
|
Copy
and paste of features |
|
Powerful configuration management for easy what if design
variations (geometrical and physical) |
|
Comprehensive support for bi-directional CAD data exchange
with most major CAD packages |
|
Comprehensive, context-sensitive HTML-based help system and
tutorials |
|
OpenGL graphics taking advantage of the latest Computer
Graphics chips |
CAD
Interoperability |
|
Native file translators to and from nearly all mechanical CAD
products on the market today: SolidWorks®, Pro/ENGINEER®, IPT
(Autodesk Inventor®), Mechanical Desktop®, Unigraphics®, PAR
(Solid Edge®), CADKEY®, IGES, STEP, Parasolid®, SAT (ACIS®),
VDA-FS, VRML, STL, DWG, DXF™, TIFF, JPG, Viewpoint,
RealityWave, HSF (Hoops) |
|
Support of seamless integrated third-party bi-directional file
translators, e. g. for CATIA®, Pro/ENGINEER®, etc. |
|
Supported standards: ANSI, DIN, ISO,GOSJIS, GB and BSI |
Part
Modeling |
|
Feature based, fully associative, parameterized solid modeling |
|
FeatureManager™ dynamic design tree (e.g. re-order, drag &
drop, etc.) |
|
In-place editing |
|
Integrated sketching (dynamic referencing) |
|
Extrudes, revolves, feature patterns, holes, etc. |
|
Advanced 3D operations, e.g. lofting, sweeping, complex
blending, filleting, etc. |
|
Advanced shelling, midsurfaces |
|
Multi-body support |
|
Advanced surface modeling: lofts and sweeps with guide curves,
fill-in holes, drag-handles for tangency control, etc. |
|
Trimming, extending, filleting, and knitting surfaces |
|
Translating, rotating, copying, and mirroring surfaces |
|
Support for creating 3D models from existing 2D data, e.g.
2D-to-3D extrusion, etc. |
|
Multiple design variations with Configuration Management,
DesignTables |
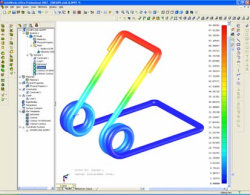 |
Assembly
Modeling |
|
Fully associative: referencing of other parts and maintaining
relationships when creating new parts |
|
Complete range of mating conditions, snap-to-fit SmartMates™ |
|
Locating conflicting mate relationships with Mate Diagnostics |
|
Dynamic assembly visualization |
|
Real-time previewing of components, parts |
|
Multiple sub-assembly support |
|
Design-in-the-context of an assembly (references to other
geometry, associative relationships, direct/indirect
constraints) |
|
Easy
designing and changing of parts and subassemblies from within
an assembly |
|
Mirrored components to create new parts and assemblies based
on existing designs |
|
Multiple assembly design variations with Configuration
Management for easy what if design scenarios |
Meshing |
|
Global and local controls for part geometry with default
sizing |
|
Mesh
control on arbitrary user defined regions |
|
Sketch line or curve meshing |
|
Free
surface meshing: quads or triangles |
|
Continuous shell (quad or tri) meshing |
|
Auto
mesh, loads and constraints update with geometry changes |
|
Mesher Status Window |
Assembly
Connectors |
|
True
surface contact |
|
Automatic contact |
|
Thermal contact resistance |
Loads
and Boundary Conditions |
|
Uniform pressure and force on faces, edges and vertices |
|
Directional pressure and force |
|
Acceleration loads (gravity) |
|
Enforced displacement and rotations |
|
Temperature, default temperature and heat flux |
|
Symmetric, antisymmetric, axisymmetric boundary conditions |
|
Fixed constraints on faces, edges and vertices |
|
Directional and prescribed constraints |
|
Thermal constraints |
|
Thermal body loads |
|
Initial temperature conditions |
|
Custom colors and sizes for loads and constraints |
Element
Library |
|
1D
line (CBEAM and CBAR) |
|
2D
linear shell (CQUAD4 and CTRIA3) |
|
2D
parabolic shell (CQUAD8 and CTRIA6) |
|
3D
linear and parabolic tetrahedron (CTETRA) |
|
Composites with plates and shells |
|
Surface to surface contact with manual or automatic
recognition of surfaces |
|
Rigid elements |
|
Conduction |
Materials
|
|
Isotropic |
|
Orthotropic |
|
Nonlinear materials |
|
-
Nonlinear elastic |
|
-
Bilinear Elasto-plastic |
|
-
Plastic |
|
Hardening |
|
-
Isotropic |
|
-
Kinematic |
|
-
Combined |
|
Yield |
|
-
Von Mises |
|
-
Tresca |
|
-
Mohr-Coulomb |
|
-
Drucker-Prager |
|
Custom stress-strain curve |
Material
Orientation |
|
Vector projection |
|
Curve tangent |
|
Rotated curve tangent |
|
Translated curve tangent |
|
Surface U and V directions |
Properties |
|
1D
beam (PBEAM) and bar (PBAR) |
|
2D
plate (PSHELL) and composite (PCOMP) |
|
3D
solid (PSOLID) |
|
Contact (BSCONP) |